Boat Problems: Our Fuel Tanks Are Trashed
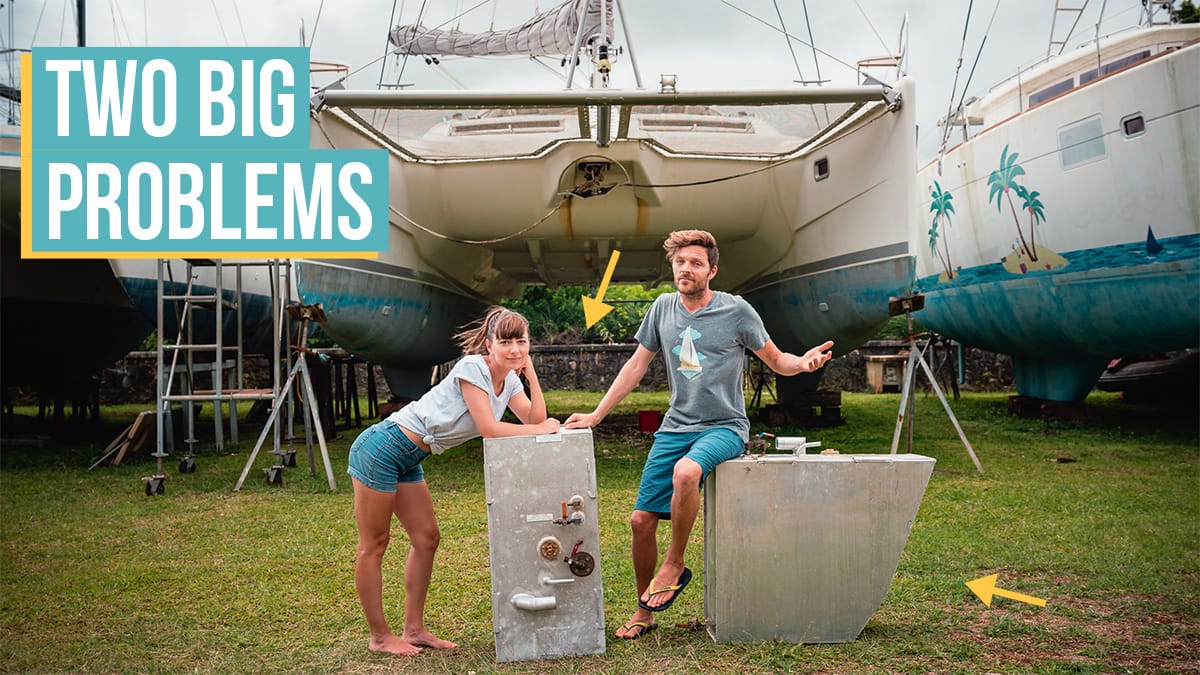
We decided to start this week off with a little break from boat work to explore a slice of our Tongan neighborhood. Because all work and no play make Jason and Nikki a dull couple. Along the journey, we meet a local boy who decides to not only be our guide but our film director too.
Then, it’s back to the boat restoration and getting our home livable again. The scrubbing continues as does the next big project: our diesel tanks. We knew our port side fuel tank was pitting and was in need of repair/replacement but we thought our starboard tank was ok. Turns out, removing our sailboat’s 15-year-old aluminum diesel fuel tanks turn into a challenge with a surprise.
Jury Rigging Fuel Tanks
Wild to think a $5 JB Weld SteelStik could be our best temporary solution – https://amzn.to/2FV7J1s
We’ve been going back and forth with what to do about these tanks and it’s been a very interesting thread topic with our Patrons (thanks for all the tips!). Obviously, we need new tanks, but ordering custom tanks and shipping them here to Tonga doesn’t make financial sense. It would take 4-5 months to create them and ship them here, plus it’s a huge risk because of the unique dimensions and custom fittings. If anything is off, the whole thing would be a complete waste.
Our plan of attack this week (unless one of you has a wildly better idea) is to use the JB Weld and fiberglass only a portion of the tank to provide extra holding for the JB Weld. Then 🤞🏼 we can shove them back in the insanely slim hole from which we pried them out. Hopefully that will keep them from leaking for a short period till we can get to NZ or AUS and have them replaced.
🙏THANK YOU!
Ups, downs and all arounds, we share it all. We’re able to do so because people like you show up each week, read, watch, comment, share, shop our gear store, and toss a tip in our production jar. If you like what you see, consider joining us on Patreon or there are lots of FREE ways you can show your support.
🎥CAMERA GEAR USED TO FILM THIS VIDEO📷
See All Of Our Photo & Video Gear here: gonewiththewynns.com/photo-video-gear
🎶MUSIC IN THIS VIDEO:
All From Artlist
- Get 2 Months FREE: https://bit.ly/artlist-GWTW
Artist – Lux Inspira, Rex Banner, J.A.K., VESHZA, Russo and Weinberg